
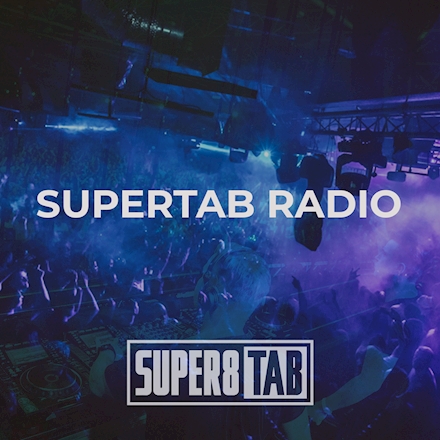
Rotational speed is increased from 2–20 rpm in steps of 2 and from 20–60 rpm in steps of 5 rpm. Replicates on other batches ensure robustness and repeatability of measurements)) with the rotating drum method GranuDrum (GranuTools, Awans, Belgium). The rheological behavior of different excipient grades and blends is evaluated ( n = 2 (Note that blends with 5% w/w, 10% w/w, 15% w/w, 25% w/w, and 40% w/w fines were measured once (n = 1) instead of in duplicate. He concluded that cohesive powder take longer to fill dies and hence could be a potential cause of tablet weight variability.
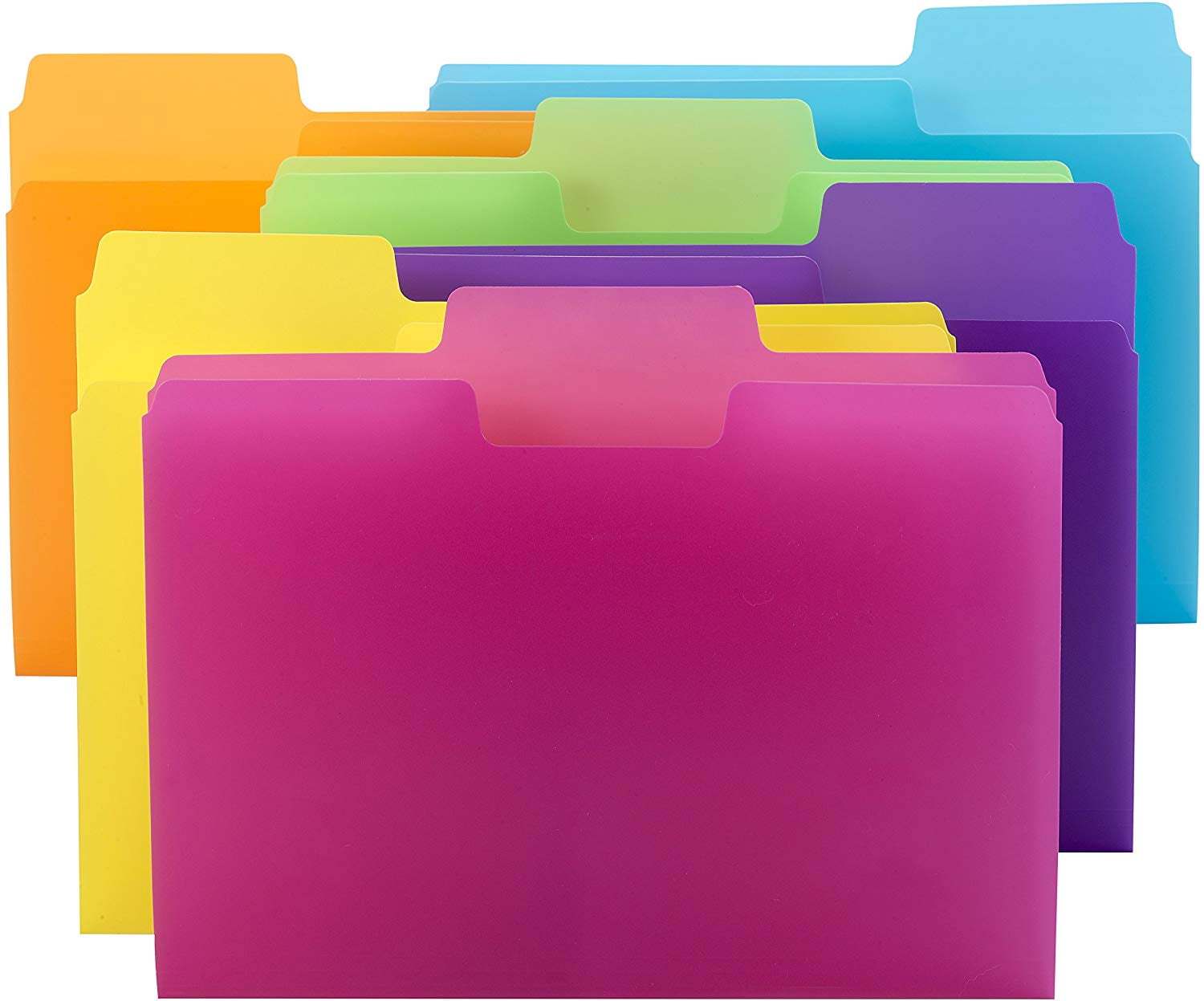
simulated the die filling process for cohesive materials. used a fixed frame and a moving die disc system to examine the effect of blend composition, shoe properties and die parameters on uniformity of die filling. He showed that powder characteristics, shoe speed, and die geometry play an important role in the die filling process. for example used transparent dies and moving feeding shoes to study the powder flow of different metallurgical powder components in air and vacuum. So far, only a few characterization techniques have been developed with specific focus to mimic the die filling process. Simple flow measurements tend to fail in the prediction of powder flow into tableting dies, due to a lack of simulation of the right flow field and stress state. This study also revealed that obtained insights on rheological behavior can be used to optimize agitator settings in a tableting machine.Īlthough many different characterization techniques have been developed, care must be taken to select the most suitable characterization technique for a specific approach. The presence of fines between larger particles turned out to reduce the rheological index, which the authors explain by improved particle separation at more dynamic flow fields. Particle size distribution was identified as a main contributing factor to the rheological behavior of powders. A new parameter for rheological behavior was introduced, which is a measure for the change in dynamic cohesive index upon changes in flow field. In the current study, the rheological behavior was investigated for a wide range of excipients with a wide range of material properties. One of the challenges in mimicking the die filling process is the impact of rheological powder behavior as a result of differences in flow field in the feeding frame. Many flow characterization techniques are present, but so far only a few have shown to mimic the die filling process successfully. With the emergence of quality by design in the pharmaceutical industry, it becomes imperative to gain a deeper mechanistic understanding of factors impacting the flow of a formulation into tableting dies.
